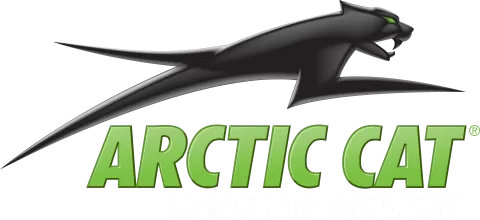
Try imagining a world without the aid of technology; it seems impossible nowadays. Technology is utilized in nearly every area of design and manufacturing around the world and has helped improve products in extraordinary ways. Parts have become quicker and cheaper to produce, all the while becoming more complex because of technology. One amazing outcome from technology enabling parts to be more advanced, while being cheaper, is that it can create a circular pattern of additionally making itself more affordable and more widely used.
Arctic Cat has an incredibly diverse portfolio of technologies that improve its products from concept to production. Listed below are some categories with a few corresponding technologies that are utilized. Arctic Cat employs many workers with these in-demand tech skills:
- Conceptualization/ Ideation
- Interactive pen computers/tablets
- Digital sketching software
- e.g., Photoshop®
- Surfacing software
- e.g., Catia®
- Design
- Solid modeling CAD
- e.g., ©Siemens NX
- Finite element analysis (FEA)
- Computational fluid dynamics analysis (CFD)
- Mold flow analysis
- Plastic injection molding
- Solid modeling CAD
- Testing/ prototyping
- 3D Printing
- Material extrusion
- Selective Laser Sintering (SLS)
- Laser cutting
- Metals and plastics
- CNC milling
- Lathe turning
- Anechoic chamber
- Noise, vibration, and harshness analysis (NVH)
- 3D Printing
- Manufacturing
- Paint line
- Rivet cell
- Robotic welding
- Quality
- Coordinate measuring machine (CMM)
- e.g., FaroArm®
- Coordinate measuring machine (CMM)
These are just to name a few of the most heavily utilized types of technologies and related skills used at Arctic Cat. There are vastly more technologies used in every aspect of the company which allows Arctic Cat to innovate, improve, and produce some of the most exciting products in the power sports industry.
To deliver on this claim, Arctic Cat Engineering utilizes many of these technologies daily. As an example, a typical part can start its life in the concept stage where it gets sketched up digitally and then modeled up in CAD. It can then get sent off for FEA to make sure the part will withstand the intense durability testing that represents what the part will experience once it goes out on a production unit. Once the part passes FEA, it can get 3D printed, installed on a prototype unit, and tested. After it passes durability testing without failure, it will be manufactured for production and then followed up by quality check. It quickly becomes apparent that producing industry-leading products requires utilizing technology to its full potential – and employing dedicated workers with top tech skills.